As we all know, the materials of stainless steel fasteners are classified into austenitic stainless steel, ferritic stainless steel and martensitic stainless steel.
The grades of stainless steel bolts are divided into 45, 50, 60, 70, and 80. The materials are mainly divided into austenite A1, A2, A4, martensite and ferrite C1, C2, and C4. Its expression method is such as A2-70, before and after "--" respectively indicate the bolt material and strength level.
1.Ferritic Stainless Steel
(15%-18% Chromium) - Ferritic stainless steel has a tensile strength of 65,000 - 87,000 PSI. Although it is still resistant to corrosion, it is not recommended for use in areas where corrosion may occur, and is suitable for stainless steel screws with slightly higher corrosion resistance and heat resistance, and general strength requirements. This material cannot be heat treated. Due to the molding process, it is magnetic and not suitable for soldering. Ferritic grades include: 430 and 430F.
2.Martensitic Stainless Steel
(12%-18% Chromium) - Martensitic stainless steel is considered a magnetic steel. It can be heat treated to increase its hardness and is not recommended for welding. Stainless steels of this type include: 410, 416, 420, and 431. They have a tensile strength between 180,000 and 250,000 PSI.
Type 410 and Type 416 can be strengthened by heat treatment, with a hardness of 35-45HRC and good machinability. They are heat-resistant and corrosion-resistant stainless steel screws for general purposes. Type 416 has a slightly higher sulfur content and is an easy-to-cut stainless steel. Type 420, with a sulfur content of R0.15%, has improved mechanical properties and can be strengthened by heat treatment. The maximum hardness value is 53-58HRC. It is used for stainless steel screws that require higher strength.
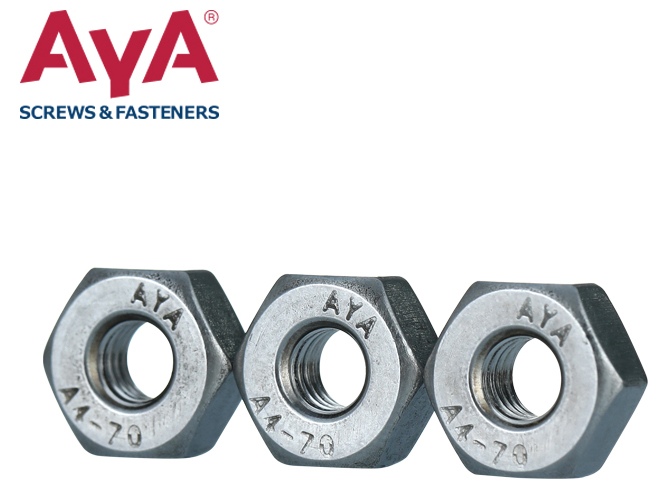
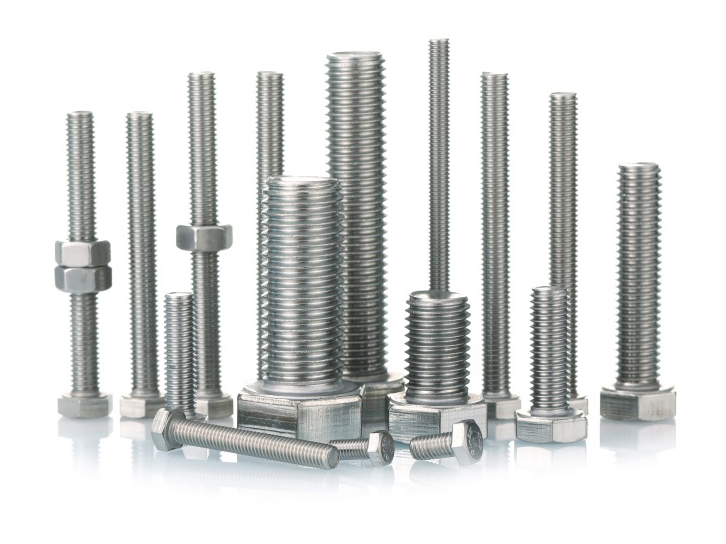
3.Austenitic Stainless Steel
(15%-20% chromium, 5%-19% nickel) - Austenitic stainless steels have the highest corrosion resistance of the three types. This class of stainless steel includes the following grades: 302, 303, 304, 304L, 316, 321, 347, and 348. They also have a tensile strength between 80,000 - 150,000 PSI. Whether it is corrosion resistance, or its mechanical properties are similar.
Type 302 is used for machined screws and self-tapping bolts.
Type 303 In order to improve the cutting performance, a small amount of sulfur is added to Type 303 stainless steel, which is used to process nuts from bar stock.
Type 304 is suitable for processing stainless steel screws by hot heading process, such as longer specification bolts and large diameter bolts, which may exceed the scope of cold heading process.
Type 305 is suitable for processing stainless steel screws by cold heading process, such as cold formed nuts and hexagonal bolts.
316 and 317 types, they both contain alloying element Mo, so their high temperature strength and corrosion resistance are higher than 18-8 stainless steel.
Type 321 and Type 347, Type 321 contains Ti, a relatively stable alloying element, and Type 347 contains Nb, which improves the intergranular corrosion resistance of the material. It is suitable for stainless steel standard parts that are not annealed after welding or are in service at 420-1013 °C.
Post time: Jul-18-2023